Accurate weight information is important for online sellers. Incorrect weight can lead to extra shipping fees, unhappy customers, and wasted resources. This blog explains methods to calculate volumetric weight and shipment weight properly.
It also covers common mistakes, the equipment used, steps to follow during measurement, and ways to review the weight data. The goal is to help online ecommerce stores maintain accurate records and cut down on unexpected costs. This will help ecommerce sellers and logistics professionals improve weight calculation in their shipping process.
Importance of Correct Weight Measurement in eCommerce
When a package is sent to a customer, its weight is a key factor for pricing. Shipping companies charge fees based on the dead weight and volumetric recorded. If the actual weight is lower than the mentioned weight slabs the seller won’t face any hiccups. On the other hand, if the recorded weight is too high, the customer may be overcharged. Both cases cause problems.
Here’s why accurate weight measurement matters:
- Helps keep shipping costs in line with expectations.
- Prevents disputes with shipping companies.
- Provides a better experience for buyers.
- Supports proper management of shipping expenses.
Understanding Volumetric Weight vs. Actual Weight
When shipping packages, carriers consider the actual and volumetric (dimensional) weights to determine the chargeable weight. Understanding the difference can help you avoid unexpected shipping costs and optimize packaging.
Actual Weight vs. Volumetric Weight
- Actual Weight: The real weight of the package, measured on a scale.
- Volumetric (Dimensional) Weight: The space a package occupies in a shipment, calculated using specific formulas based on the shipping mode.
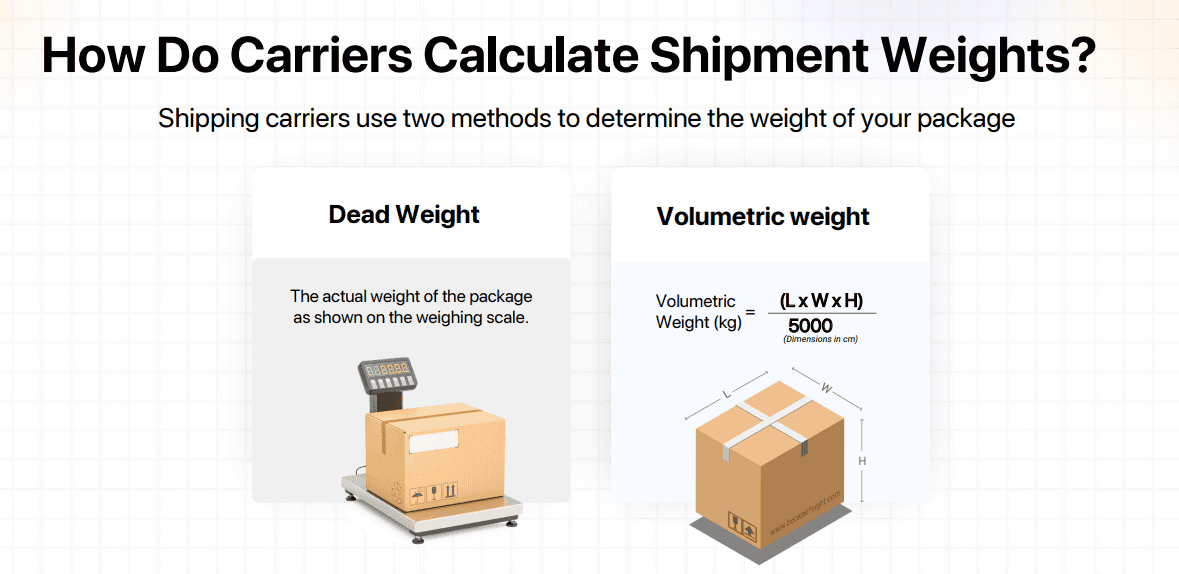
What is Chargeable Weight?
Chargeable weight is the greater of the actual weight and volumetric weight. If a package is lightweight but large, its volumetric weight will be higher, and the carrier will charge based on that instead of the actual weight.
Example: A lightweight pillow in a large box may have an actual weight of 3 kg, but if its volumetric weight is 7 kg, the shipping cost will be calculated based on 7 kg.
How to Calculate Volumetric Weight for Different Modes of Transport?
Different carriers use different divisors to calculate volumetric weight. While UPS and FedEx typically divide by 5,000, the International Air Transport Association (IATA) originally set the standard at 6,000 – based on the average weight of 1 cubic metre of freight, approximately 166.7 kg. Here are the standard formulas for different shipping methods:
Air Freight: 1:6 Density Ratio
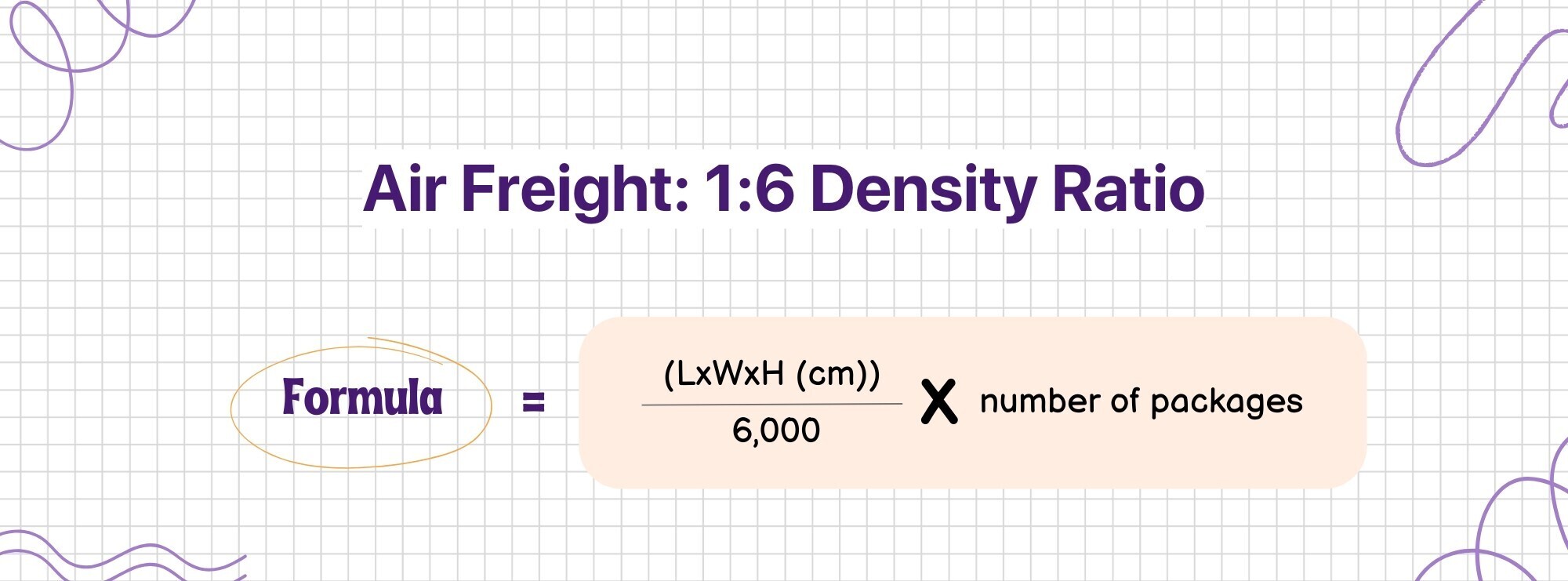
Ocean Freight: 1:1 Density Ratio (For LCL shipments)
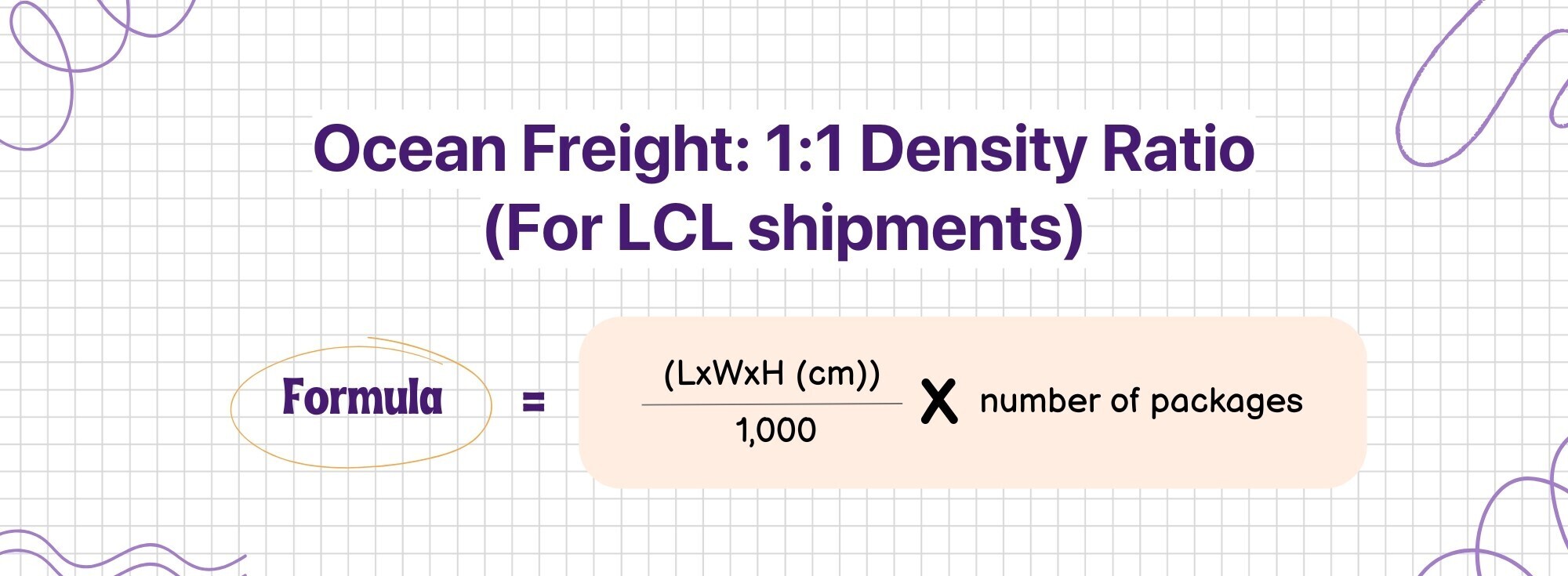
Rail Freight: 1:3 Density Ratio
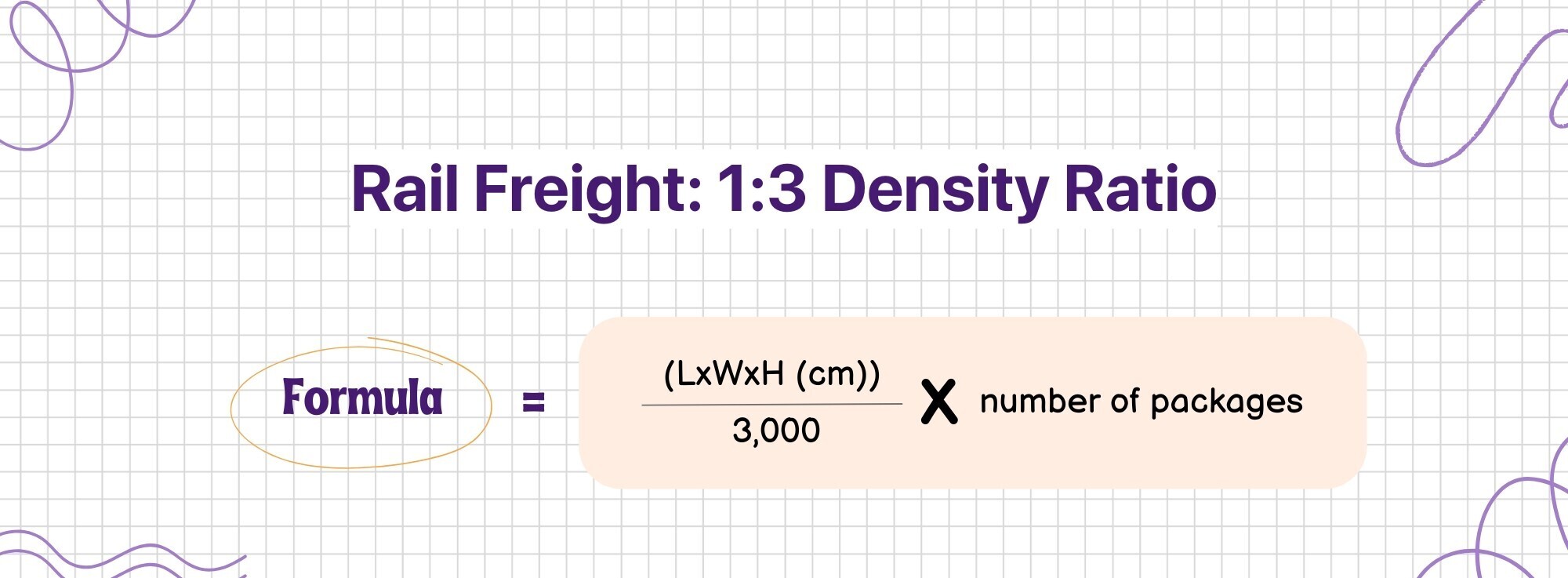
What are the Steps to Calculate Shipment Weight Correctly?
A clear procedure can help keep weight data accurate. The following steps provide a guide for calculating shipment weight:
1. Prepare the Equipment
- Inspect the Scale: Check for visible damage or debris on the scale surface and make sure the display is clear.
- Zero the Scale: You can use the tare function to account for container weight.
- Calibrate the Scale: Use standard weights to test the scale and document the calibration process in a logbook.
2. Weighing the Item
- Place the Package Carefully: Put the item in the center of the scale. Avoid touching the sides or moving them during measurement.
- Read the Display: Wait until the reading stabilizes before noting the weight.
- Record the Weight: Enter the number into your system or note it on a paper form. If possible, have a second person verify the reading.
3. Account for Packaging
- Weigh the Packaging Material: Measure the weight of boxes, tape, and padding separately.
- Subtract Packaging Weight: If the shipping cost is calculated on the item weight alone, then you need to subtract the weight of the packaging from the total weight.
- Combine Data: Record both the weight of the item and the total weight with the packaging. This data helps track the contribution of each element to the total weight.
4. Verification and Quality Checks
- Double-Check Measurements: Have another employee reweigh the item periodically.
- Use a Checklist: Follow a written checklist that details every step.
- Spot-Check Regularly: Randomly select packages for a second measurement.
- Document Discrepancies: If there is a difference between the two measurements, note it and check for equipment issues.
5. Recording Weight Data
Maintaining clear records is as important as taking the measurement correctly. You can do that using manual or digital logs. Manual logs use paper logs to record weight, date, and operator name. While in digital records, you need to enter weight data into a database. Ensure that the data entry process is error-free.
6. Regular Data Review
- Daily Checks: At the end of each day, review the recorded data for any obvious errors.
- Weekly Summaries: Compile a report on weight data over the week. Look for trends or repeated discrepancies.
- Monthly Audits: Conduct a formal audit of equipment calibration logs and weight records.
- Feedback Meetings: Hold sessions with the team to discuss any issues. Note suggestions for reducing errors further.
Following these steps consistently helps reduce errors and maintain accurate records.
7. Using Software Tools
Software can help keep track of weight data. A good system will:
- Store all weight entries in a central location.
- Provide graphical displays of trends over time.
- Send alerts when a reading is out of the ordinary.
After keeping detailed records and reviewing them regularly, errors can be caught early and fixed.
Factors That Can Cause Weight Differences
Weight differences can occur at several points in the process. Here are some common causes:
- Data Entry Errors: Mistakes when entering data can lead to incorrect numbers.
- Faulty Equipment: Outdated or unmaintained scales may give incorrect readings.
- Improper Packaging Practices: Varying packing materials or techniques can change the overall weight of the shipment.
- Environmental Conditions: Temperature or humidity changes may affect some weighing devices.
- Handling Errors: Placing the package incorrectly on the scale or not zeroing the scale can lead to errors.
Understanding these factors helps you target the steps needed to cut down on mistakes.
What are the Tools and Equipment Needed for Accurate Weight Calculation?
Using the right tools ensures accurate weight calculation for shipments, with various devices suited for different item types. Digital scales offer quick and portable readings for everyday use, while platform scales provide a larger surface for heavier packages. Precision scales are ideal for small or delicate items requiring fine measurement, and industrial scales handle heavy loads and multiple items at once.
Regular calibration is essential to maintain accuracy. Certified calibration weights help adjust scales on a set schedule, electronic calibration systems allow automatic adjustments, and manual calibration kits assist technicians in fine-tuning older devices.
Automated measurement systems further reduce errors by integrating scales with software, where integrated software directly transfers weight data into order management systems to minimize manual entry mistakes. In larger operations, robotic weighing devices streamline the process by handling items without human contact, reducing handling errors and improving efficiency.
How to Reduce Shipping Costs with Accurate Weight Measurement?
A few best practices can help lower the chances of errors. The list below shows actions that can be taken:
- Consistent Equipment Use: Use the same scale for similar products. This consistency reduces variation.
- Regular Training: You need to make sure that all team members know how to use the equipment. Hold periodic sessions to review procedures.
- Set Standard Operating Procedures: Write clear instructions for every step. Use checklists to ensure that nothing is missed.
- Monitor Environmental Conditions: Keep scales in a place with stable temperature and low dust. Avoid areas where vibrations may occur.
- Document Every Step: Use a logbook for calibration, measurements, and quality checks.
- Review and Update Procedures: Make changes when new issues appear. Ask staff for ideas on how to improve the process.
- Conduct Regular Maintenance: Clean scales and check for wear. Replace equipment that is not working correctly.
Following these practices will help cut down on mistakes and keep weight records accurate.
Most Common Weight Calculation Mistakes and How to Avoid Them?
1. Inaccurate Calibration
- Mistake: Failing to calibrate the scale or calibrating it incorrectly.
- Solution: Set up a regular calibration schedule. Use certified weights and record each calibration.
2. Incorrect Taring
- Mistake: Sometimes forgetting to reset the scale to zero before weighing an item can give this error.
- Solution: Use the tare function for any container or packaging.
3. Poor Packaging Practices
- Mistake: Using inconsistent packaging methods that add extra weight unpredictably.
- Solution: Standardize the type of packaging for similar items. Measure and record the weight of common packaging materials.
4. Data Entry Errors
- Mistake: Typing the wrong number or misreading the display.
- Solution: Double-check the reading before recording it.
Use software tools to capture data automatically when possible.
5. Inconsistent Measurement Techniques
- Mistake: Placing items off-center or moving them while the scale is in use.
- Solution: Follow a set procedure for placing each item. Train staff to wait until the reading is stable before noting the weight.
6. Recording Packaging Weight Separately
- Mistake: One area where mistakes often occur is in accounting for the packaging weight.
- Solution: Before packing an item, weigh the box, bubble wrap, and materials. Write down the standard weights for each type of packaging and subtract the packaging weight from the total. If you change the type of packaging, re-measure and record the new weights. Make sure everyone understands the importance of keeping packaging weight separate.
How to Improve Accuracy?
A few extra tips can help further reduce weight errors in your process:
- Use Consistent Timing: Weigh items at the same time each day when conditions are similar.
- Avoid Interruptions: Ensure the weighing area is free from disturbances like heavy foot traffic.
- Monitor Equipment Performance: Keep a record of calibration results and repair needs.
- Simplify the Process: The fewer steps there are, the lower the chance of mistakes.
- Encourage Team Communication: Let team members report any issues or ideas to improve the process.
- Set Clear Guidelines: Write out instructions that every employee must follow.
- Regularly Update Technology: Keep software and hardware current to reduce errors from outdated systems.
Following these tips will help maintain accurate product weight measurements over time.
How to Train Your Staff on Accurate Weighing?
An informed team is key to correct weight calculation. Here are suggestions for training:
- Create Simple Manuals: Write step-by-step instructions that are easy to follow.
- Hold Regular Sessions: Organize short meetings to review procedures and answer questions.
- Demonstrate the Process: Show new employees how to use the scale and record data.
- Encourage Peer Checks: Have team members verify each other’s measurements.
- Offer Refresher Classes: Periodically review best practices with the whole team.
- Provide Visual Aids: Use charts and photos that illustrate the proper method.
- Track Performance: Monitor error rates and praise careful work.
Training your staff helps reduce mistakes and builds a strong system.
How to Manage Weight Discrepancies for Multiple Product Sizes and Variations?
Different items may require special handling during weight calculation. Consider these points:
- Small and Lightweight Items: Use a precision scale for very small items to capture even slight differences.
- Fragile Items: Make sure the item is placed securely on the scale without risk of damage.
- Bulk or Irregular Items: If an item has an unusual shape, make sure it sits flat on the scale.
- Multiple-Item Shipments: Weigh each item separately if possible. If not, note that the combined weight may need extra checks.
- Packaging Variations: Record the weight of each type of container or filler material separately.
Real-Life Benefits of Accurate Weight Calculation
When weight is measured correctly, many parts of the business see improvements. Some benefits are:
- Reduced Shipping Fees: The correct weight prevents unexpected charges from carriers.
- Lower Customer Complaints: When the shipping cost matches the actual weight, customers are more satisfied.
- Better Inventory Management: Accurate weight data helps in tracking stock and planning orders.
- Smooth Billing Processes: Fewer disputes with shipping companies mean an efficient process.
- Time Savings: When fewer errors occur, staff spend less time on corrections and more on other tasks.
- Improved Record Keeping: Detailed logs help identify issues and allow for quick action.
Detailed Checklist for Accurate Weight Calculation
Below is a checklist that you can use every time you calculate shipment weight:
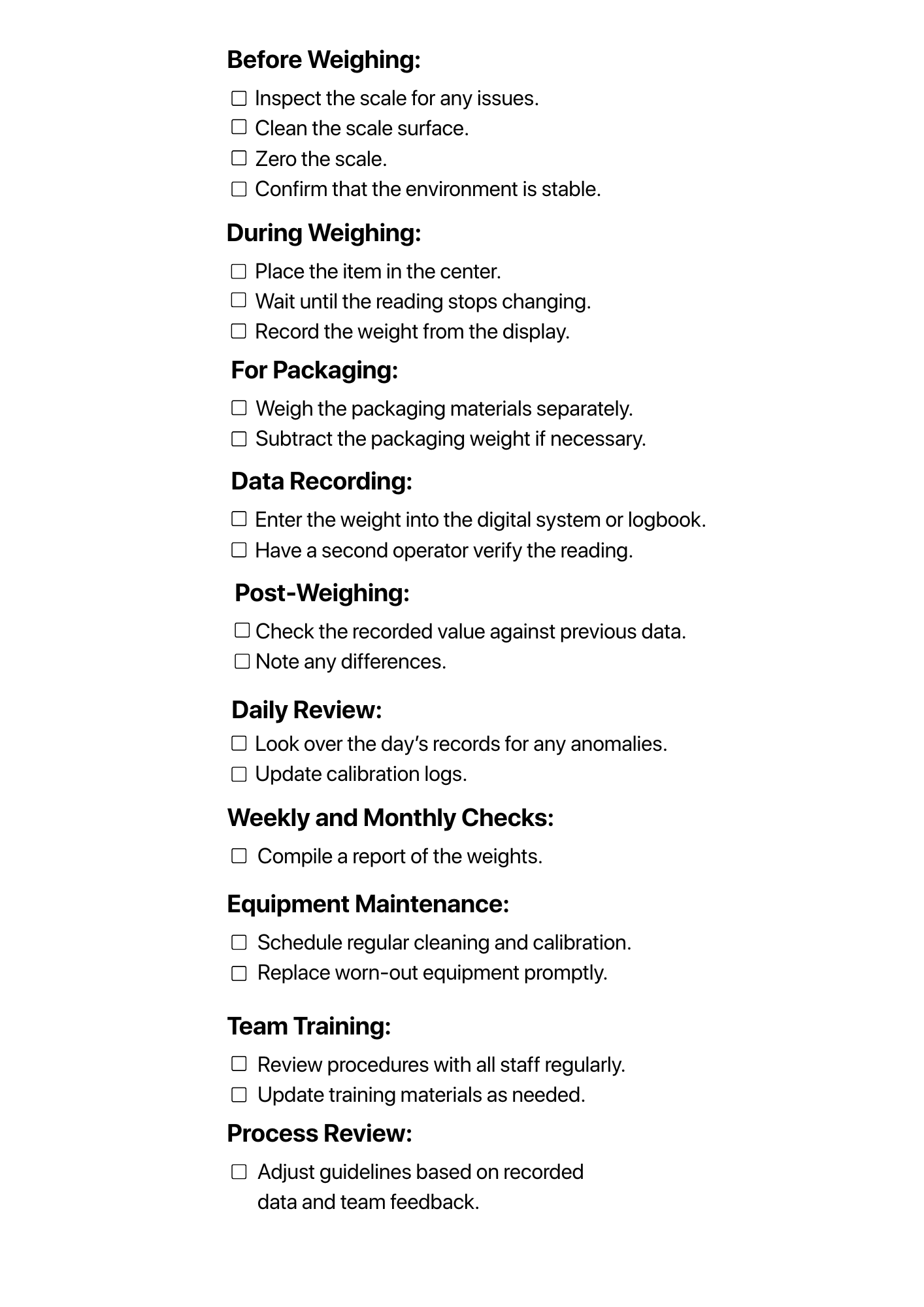
Using this checklist will help maintain the accuracy of every shipment weight calculation and tracking SLA breaches. You can print these to include in your inventory or training process, or SOPs.
How to Adapt When Issues Arise?
No process is free of errors. When mistakes occur, a quick response helps reduce the impact:
- Identify the Problem: Check the records to see where the error occurred.
- Investigate the Cause: Review the equipment logs, packaging records, and staff reports.
- Take Corrective Action: Adjust the measurement procedure. Recalibrate the scale if needed.
- Notify the Team: Inform everyone about the change to prevent future errors.
- Document the Change: Keep a record of what was changed and why.
- Review Impact: Look at future data to see if the correction worked.