Weight discrepancies are a common yet often overlooked issue in eCommerce shipping. It is the basic metric that influences your shipping costs, packaging expenses and overall profit. Knowing accurate product weight calculation is crucial for smooth shipping operations in the e-commerce industry.
In fact, weight discrepancies can impact up to 20% of your shipments, leading to challenges in managing logistics budgets and potential cash flow problems. Fortunately, by implementing strategic measures and leveraging the right technologies, you can effectively minimize these weight discrepancies.
In this guide, we will explore why these discrepancies occur, how they affect your shipping costs, and practical ways to reduce weight discrepancies and streamline your logistics operations.
What is weight discrepancy?
First, let’s start by discussing what weight discrepancy actually means.
Weight discrepancies occur when the weight measured by your business differs from the weight recorded by the courier service. These inconsistencies typically arise due to varying measurement methods, equipment sensitivity, or packaging differences.
Simply put, a weight discrepancy occurs when there’s a difference between the weight measured by the online store and that recorded by the shipping company.
Even minor discrepancies can result in significant additional costs or delays, making it essential to address them effectively. It often happens due to variations in how weight is measured or recorded at different stages of the shipping process by different courier companies.
For example, an ecommerce brand might measure the weight of a package using their in-house equipment, but when the package reaches the courier’s facility, the weight recorded by the courier’s more sensitive scales may differ.
These differences, though sometimes small, can accumulate and result in significant additional shipping costs or delays.
Common Causes of Weight Discrepancies:
- Inaccurate Volumetric Weight Calculations: Miscalculating dimensional weight using incorrect measurements or divisors (e.g., 5000 or 4000).
- Inconsistent Packaging Materials: Variations in packaging materials can cause fluctuations in shipment weight.
- Human Error: Improper handling or failure to zero scales before weighing.
- Equipment Variability: Differences in weighing equipment accuracy between the e-commerce business and courier facilities can lead to inconsistent weight readings, resulting in billing discrepancies or disputes.
How Do Carriers Calculate Shipment Weights?
Now, let’s understand how courier partners calculate weight. They generally use two primary methods to calculate the weight of a shipment:
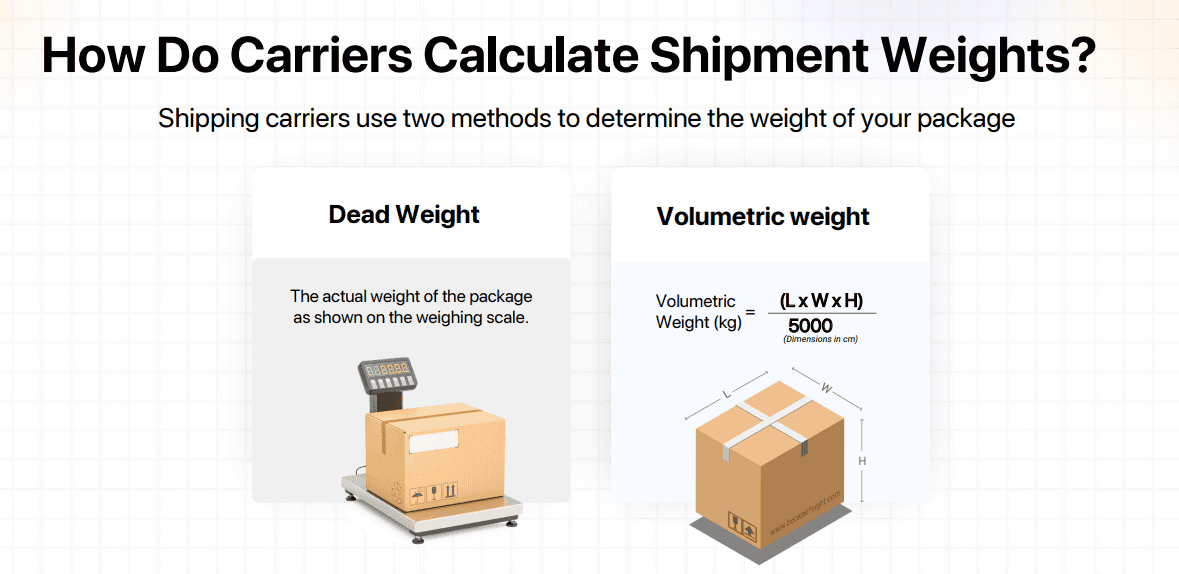
1. Dead Weight
This is the actual weight of the package as shown on a weighing scale.
2. Volumetric Weight
It is determined by the amount of space the package occupies. It is calculated using the formula:
(Length × Breadth × Height) / 5000 (in cm)
The higher of the two values is used to calculate your shipping charges along with factors like pincode, carrier partner, delivery speed, etc.
Why Does This Matter?
If your package is larger but lightweight, the volumetric weight may exceed the actual weight, resulting in higher charges. Additionally, inaccuracies in package dimensions or weights can lead to discrepancies and unexpected costs.
Top Strategies to Reduce Weight Discrepancies
Product weight discrepancies are a long-fighting battle that ecommerce companies try their best to win. Here are some effective strategies to minimize weight discrepancies and streamline your shipping process:
1. Weight Measurement Accuracy
1. Accurate Volumetric Weight Calculation:
To reduce shipping weight discrepancies, accurately calculating the volumetric weight of your shipments is essential. Start by carefully measuring the length, breadth, and height of the package. Then, divide the result by the appropriate divisor, as specified by your courier partner.
It’s also essential to ensure that the packaging is proportional to the product; oversized packaging can lead to unnecessarily high volumetric weights, increasing shipping costs. By meticulously following the measurement process, you can ensure accurate product weight measurement that closely matches the courier partner’s records, minimizing the risk of discrepancies.
2. Implement Standardized Measurement Processes:
Inconsistent measurement practices across different stages of the supply chain are a leading cause of product weight discrepancies. To address this issue, it’s essential to implement standardized measurement processes throughout your operation.
This includes using calibrated weighing scales or scientific scales, establishing clear guidelines for weighing procedures, and training employees on proper measurement techniques. By standardizing these processes, you ensure that every product is measured accurately and consistently, reducing the potential for discrepancies and lowering shipping costs for your business.
3. Invest in Automated Weighing Systems:
Investing in automated weighing systems can significantly improve the accuracy of your product measurements. These systems use advanced technologies, such as load cells and digital sensors, to provide precise weight readings with minimal human intervention.
Automated systems are particularly useful in high-volume operations, where even small errors in weight measurement can add up over time. By automating the weighing process, you can reduce labor costs, improve operational efficiency, and ensure that your weight measurements are consistently accurate, minimizing the risk of discrepancies.
2. Record Management & Data Analysis
1. Maintain Image Records of Orders:
Keeping a visual record of your shipments is an invaluable practice. By photographing the packaged product, including its dimensions and packaging materials, you create a visual reference that can be used in case of disputes with your courier partner.
These images serve as evidence to support your claims about the product’s weight and dimensions, making it easier to resolve any discrepancies that arise. Additionally, maintaining a catalog of these records can help you track and review past shipments, identifying patterns or recurring issues that need to be addressed.
2. Monitor and Analyze Data:
Data monitoring and analysis are critical for identifying trends, patterns, and root causes of product weight discrepancies. By using data analytics tools and software, you can track key metrics such as average product weights, variance levels, and the frequency of discrepancies. Analyzing this data allows you to identify areas where discrepancies are most likely to occur and take targeted actions to address them.
For example, if certain products consistently show weight discrepancies, you can investigate the underlying causes and implement corrective measures to ensure consistency. Regularly monitoring and analyzing data also helps you stay ahead of potential issues and continuously improve your shipping processes.
3. Packaging Strategies
1. Map Packaging with SKUs:
Mapping specific packaging materials to product SKUs (Stock Keeping Units) is a good way to ensure consistency in your shipping processes. By associating each SKU with a specific type of packaging in the right-sized boxes, you standardize the weight and dimensions of shipments, reducing the likelihood of discrepancies.
This practice is especially useful for products that are shipped frequently or in large volumes, as it ensures that each package is treated uniformly. Over time, this consistency helps build a reliable database of product weights and lightweight packaging materials, streamlining the shipping process and reducing errors.
2. Optimize Packaging Materials and Methods:
Variations in packaging materials and methods can contribute to weight inconsistency, particularly in industries that use lightweight materials or non-standardized materials. To address this issue, it’s important to optimize your packaging strategy to ensure consistency and accuracy.
This may involve standardizing packaging designs, implementing weight-saving measures, and conducting packaging audits to identify areas for improvement. For example, switching to more consistent packaging materials or reducing excess packaging can help standardize the weight of your shipments, reducing the likelihood of discrepancies.
4. Shipping Technologies & Solutions
1. Outsource E-Commerce Fulfillment:
Outsourcing your ecommerce fulfillment operations to a third-party logistics provider (3PL) can offer significant advantages in managing weight discrepancies. Many 3PLs have access to advanced weighing machinery and automated systems that ensure precise product measurements.
These providers also often use technology-driven processes that reduce the potential for human error, ensuring faster and more accurate order fulfillment. By outsourcing fulfillment, you can also benefit from the expertise of professionals who specialize in logistics, allowing you to focus on other aspects of your business while minimizing the risk of costly weight discrepancies.
2. Opt for a Shipping Solution:
Using a reliable shipping solution, like Shipway, can streamline the management of weight discrepancies. These platforms provide ecommerce businesses with tools to track and manage discrepancies, upload images of shipments, and resolve disputes directly with courier companies.
By centralizing these tasks within a single platform, you can monitor your shipments more effectively and take proactive steps to address any issues that arise. Additionally, these solutions often offer analytics and reporting dashboards that can help you identify trends in weight discrepancies and make informed decisions to improve your shipping processes.
3. Utilize Weight Verification Technologies:
Weight verification technologies, such as Checkweighers and dimensional weighing systems, provide an effective means of verifying product weights and detecting discrepancies in real time. These systems use advanced sensors and algorithms to compare measured weights against predefined criteria, alerting operators to any deviations.
By integrating these technologies into your operations, you can proactively identify and prevent weight discrepancies before they lead to costly errors or operational delays. This not only improves the accuracy of your shipping processes but also enhances the reliability of your overall supply chain.
5. Training, Inspections & Communication
1. Conduct Regular Audits and Inspections:
Random weight audits and inspections are crucial for identifying and addressing potential sources of weight variations. By periodically reviewing your weighing equipment, packaging materials, and inventory records, you can detect any issues that might contribute to discrepancies before they impact your operations.
For example, if a particular scale is found to be consistently inaccurate, replacing or recalibrating it can prevent future discrepancies. Audits also provide an opportunity to review your measurement processes and ensure that they comply with industry standards, helping to maintain the accuracy and reliability of your shipping operations.
2. Train Employees on Shipment Handling and Weighing Procedures:
Human error is a common cause of product weight discrepancies, often resulting from inadequate training on handling and weighing procedures. Investing in comprehensive training programs for your employees can help reduce these errors and improve overall efficiency.
Training should cover key topics such as accurate weight measurement, proper handling techniques, and adherence to established protocols. By ensuring that your employees are well-trained and knowledgeable, you can minimize the risk of errors and enhance the accuracy of your shipping processes.
3. Establish Clear Communication Channels:
Effective communication is essential for addressing weight discrepancies and resolving issues quickly. Establishing clear communication channels between different departments, suppliers, and logistics partners ensures that everyone involved in the shipping process is on the same page.
This includes providing mechanisms for reporting and resolving discrepancies, as well as implementing escalation procedures for handling urgent issues. Employing a transparent culture and accountability, you can ensure that weight discrepancies are addressed promptly and efficiently, minimizing their impact on your D2C business.
How Shipway Helps Reduce Weight Discrepancies?
Shipway offers tools and support to minimize weight discrepancies, ensuring accuracy and transparency:
1. Image Verification
Compare package images with Airway Bills (AWB) to validate dimensions and weights.
2. Historical Weight Tracking
Access past shipment data to track and maintain consistency in weight measurements.
3. Product Content Verification
Ensure the shipment’s content, SKUs, and quantities match the provided data for accurate billing.
4. Sample Image Verification
Verify sample images of SKUs or similar products to ensure accurate weight and dimension assessments.
5. Quick Dispute Resolution
- Submit disputes via the Shipway dashboard within 7 days of identifying a discrepancy.
- Resolutions are typically provided within 72 hours, with escalation options if required.
6. Dedicated KAM Support
Shipway provides a dedicated Key Account Manager for businesses with 100+ orders. Your KAM will provide you with dedicated support and ensure the best solution for your business by reviewing and comparing sorter and sample images.
Conclusion
Product weight discrepancies can pose significant challenges for e-commerce businesses, impacting operational efficiency, profitability, and customer satisfaction. However, by implementing the weight discrepancy management strategies outlined above, you can effectively reduce these discrepancies and optimize your shipping processes.
Embracing these strategies, opting for the right shipping aggregation solution and continuously improving your processes, ensures that your ecommerce business runs smoothly, your shipping costs are optimized, and your customers remain satisfied.
Common Seller Queries and Solutions:
A
Why are additional charges applied when the actual weight is under the slab?
Your shipping cost for a package is based on the weight and dimensions mentioned in the sorter images. Verify with documented package images and raise a dispute on the Shipway dashboard incase of discrepancies.
Images shared by the courier do not match my parcel. What should I do?
Shipway’s KAM (Key Account Manager) reviews discrepancies, analyzes your historical shipping cost and package weight, and resolves the weight dispute within 72 hours.
What if the courier partner doesn’t share images?
Shipway’s support team escalates the issue to the relevant courier partner and resolves disputes on your behalf.